
Is Tencel (aka Lyocell) A Sustainable Fabric? The Textile Test Series Investigates
It’s quite unbelievable the countless steps clothing goes through before entering your closet (fabric production, dying, finishing, cutting, sewing, labelling, shipping and more). But let’s break down just a fraction of that process: the fabric, which is the foundation of all garments. It must be grown (or manufactured in a factory), processed into thread, and woven, all before it reaches the designers hands where creativity and creation comes into play. Silhouette, vibe and mood are all translated through the language of the fabric. In this series, Textile Test, we will investigate the life-cycle of different fabrics from plant to final product and beyond.
A Solid Reputation
Soft, renewable, biodegradable and wrinkle-resistant, lyocell, or Tencel©, is considered an eco-textile with big advantages. It’s created through an award-winning closed-loop production process, and uses resources certified by the Forest Stewardship Council. In 2000, the European Union awarded the Tencel manufacturing process an Environmental Award in “technology for sustainable development.”
How It’s Made
Lyocell is a biodegradable fiber made from eucalyptus trees. The eucalyptus tree, an extremely fast-growing resource requires low water and virtually no pesticide inputs to grow—a nice break from resource-intensive cotton.
Once the eucalyptus trees are harvested, mostly from sustainable farms, the wood is soaked in a non-toxic solution called amine oxide. Amine oxide is a petrochemical solution but 99.5% is reclaimed, purified and reused again and again. (Since the solvent in non-toxic, the small amount that is not reused is considered not to be hazardous.) The goal of soaking the wood pulp in the solution is to extract raw cellulose—a large part of the cell wall (remember high school biology? This is the part of the cell that holds everything together. And it also happens to be the most common organic compound on Earth).
So water and wood go into the factory and fiber comes out.
Lyocell’s Lifecycle
Once the fiber is made, because it comes from trees, the textile itself is biodegradable. It is estimated, under the right conditions, that the textile can take up to 6 weeks to decompose in compost. That would be a fun science project!
Lyocell’s characteristics beyond the manufacturing process are also resource-saving. The fibers are a pure white color, with a soft and almost silky texture that doesn’t need to be bleached. It’s also highly absorbent to dyes, which therefore spread faster and with brighter color, so producers can use less dye and get more bang for your dip.
The final product is breathable, strong, great for draping, and wrinkle-resistant—heck yeah! Designers often use the fabric for dresses, shirts, jeans or even bedsheets.
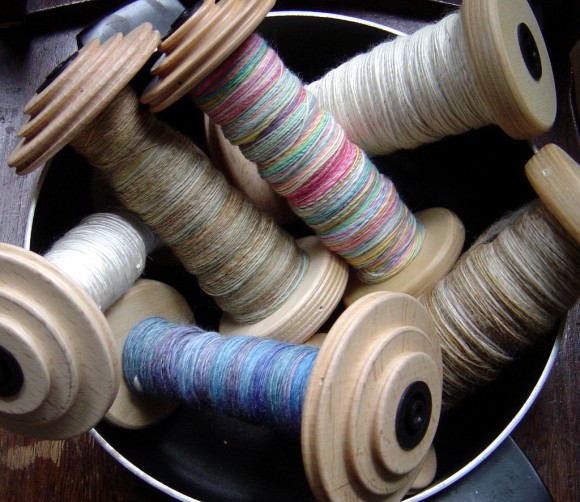
Caveat: Energy
The fiber itself is an eco-rockstar. The downside is the manufacturing process is energy intensive. An option being explored is the use of renewable energy to run the manufacturing facilities.
Patagonia, Amour Vert, and H&M are some of the many labels that use Lyocell in their garments.
Our verdict is that lyocell is a worthy contender in the world of lower-impact fabrics, and one that designers like to work with too.
Read up on other fabrics in our Textile Test Series below:
Is Bamboo a Sustainable Textile Fraud?

